La technologie d'impression 3D fait de plus en plus partie de toute pratique clinique, y compris la fabrication d'orthèses cheville-pied (AFO). Vous vous demandez peut-être si vous devez l'adopter dans votre pratique ?
Il n'y a pas de réponse simple à cette question. La technologie peut s'améliorer chaque jour, mais vous pouvez toujours prendre en compte l'efficacité, le processus et les résultats d'une AFO traditionnelle ou fabriquée manuellement et d'une AFO imprimée en 3D.
C'est pourquoi nous avons décidé de mettre côte à côte la pratique clinique traditionnelle de fabrication d'orthèses et le flux de travail numérique 3D. Nous comparerons le temps, le flux, les matériaux et les outils utilisés dans les deux processus. Nous discuterons également de ce que chacun d'eux signifie pour votre pratique.
En voici un bref aperçu :
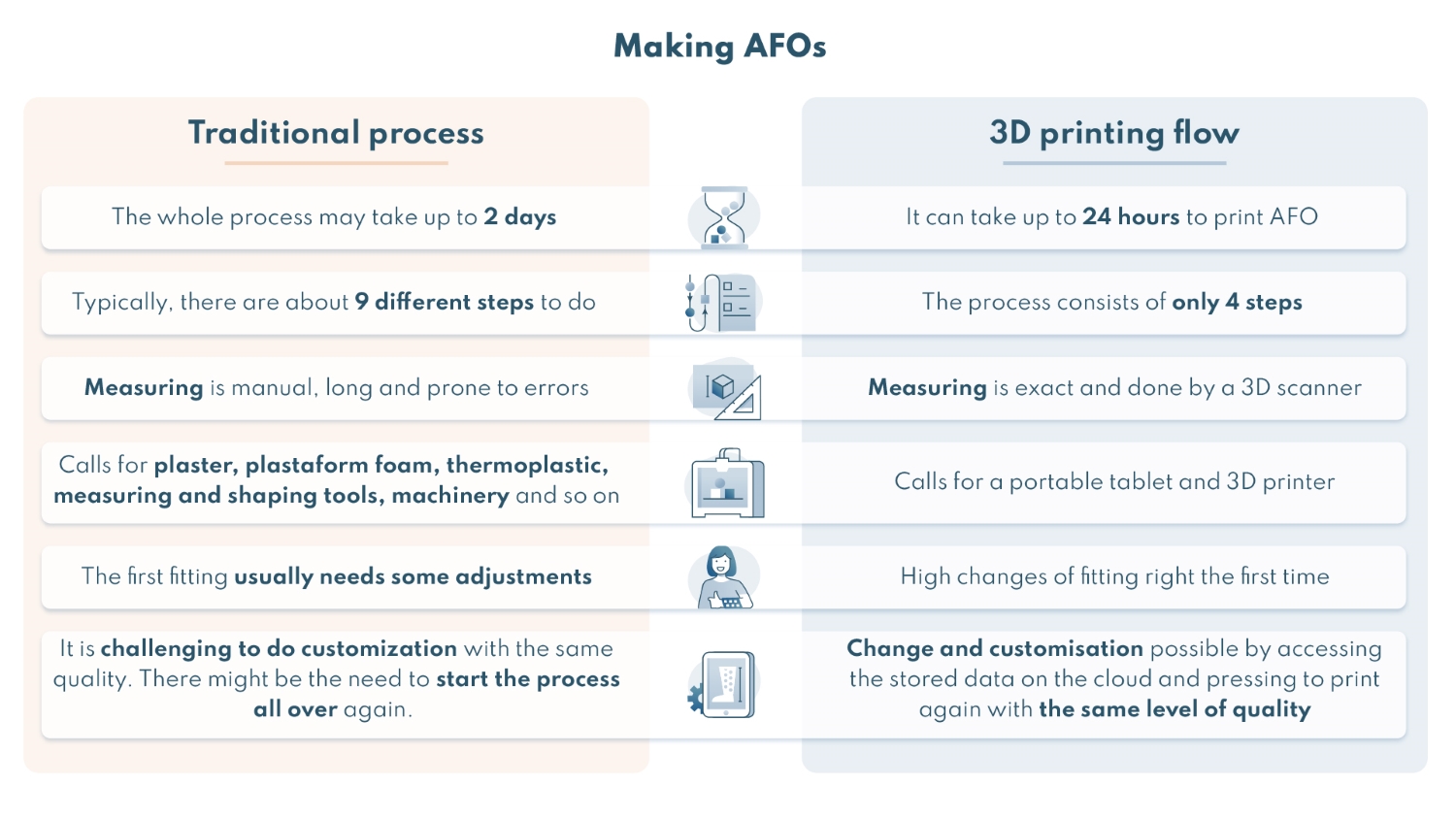
Fabrication d'orthèses conventionnelles
Examinons le processus typique de fabrication manuelle d'une orthèse :
1. Mesure de
Le processus commence par l'isolation du membre par les techniciens orthopédistes à l'aide de vaseline ou de film alimentaire afin de préserver les poils du corps lors du retrait ultérieur de l'empreinte. La prise de mesures de la partie du corps est l'étape la plus importante. Pourtant, cette seule étape peut prendre jusqu'à une demi-heure, y compris la mise en place et le nettoyage.
2. Placer des marqueurs
Ensuite, le technicien indique les marqueurs osseux avec un crayon sur la peau du patient. Il fixe ensuite le tube sur le membre du patient à l'aide de ruban adhésif, qui servira d'espace de coupe plus tard dans le processus.
3. Moulage
Vient ensuite le processus de moulage. Pour les orthèses compliquées, cela peut prendre jusqu'à dix heures. La mise en forme de l'empreinte consiste à fermer la ligne de coupe avec des pansements en plâtre et à isoler le moule négatif.
4. Moule positif et séchage
Ensuite, le technicien place une longue tige en acier au milieu de l'orthèse pour en assurer la stabilité, tout en remplissant l'empreinte négative avec du plâtre liquide. Nous avons maintenant un moule positif. Une fois encore, l'empreinte doit sécher, ce qui prend entre deux et quarante-huit heures.
5. Corriger et polir
L'étape suivante consiste à corriger et à polir le moule positif. Il s'agit d'un processus risqué qui peut diminuer la précision du moule et potentiellement le casser. Pourtant, il s'agit d'une étape cruciale dans la préparation de la fabrication des orthèses.
6. Enlever le moule négatif
Une fois que la forme positive est sèche et lisse, le technicien orthopédiste peut commencer à retirer le moule négatif. La mousse Plastazote ou plastaform est ensuite agrafée sur le modèle, et le thermoplastique est tiré par-dessus.
7. Chauffage des thermoplastiques
Le thermoplastique est ensuite chauffé dans le four. Le four rend le matériau PP, PE ou copolymère flexible afin que le technicien orthopédiste puisse le mouler sur le modèle.
8. Enlever le moule
Enfin, le technicien retire le moule du modèle et en lisse les bords.
9. Ajustement initial
C'est à ce moment-là que nous sommes enfin prêts pour l'adaptation initiale de l'orthèse. Habituellement, quelques ajustements sont nécessaires, ce qui peut prendre un certain temps. Lorsque les ajustements nécessaires sont nombreux, il peut s'avérer nécessaire de changer complètement l'orthèse. Dans ce cas, le technicien peut être amené à recommencer le processus depuis le début.
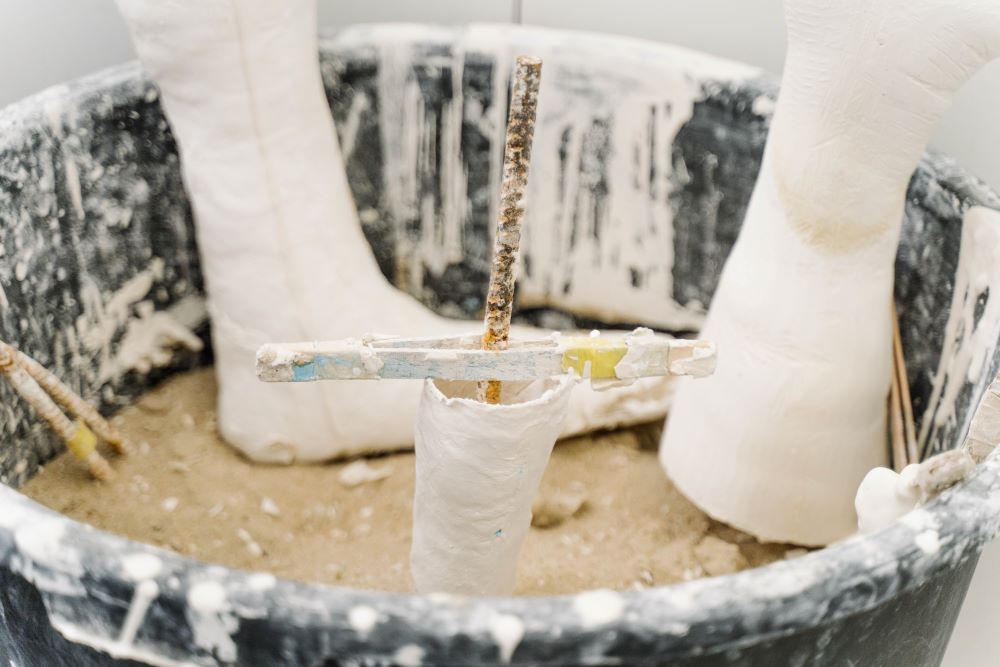
Il est temps de comparer cela avec le flux de travail numérique 3D.
Flux de travail pour les orthèses imprimées en 3D
Le processus de travail numérique ne comporte que quatre étapes : la numérisation, la modélisation, l'impression et le nettoyage.
Voici un aperçu plus détaillé :
1. Numérisation
Le processus commence par un scanner du membre pathologique. Il s'agit de positionner le membre et de réaliser le scanner. Le technicien ajoute les repères tout en rectifiant le scan, ce qui ne prend généralement pas plus de quelques minutes. Pour les orthèses compliquées ou les membres comportant plusieurs repères, cela peut prendre un peu plus de temps. Toutefois, la solution de numérisation en 3D permet d'obtenir des mesures plus exactes sans les difficultés liées aux moules traditionnels.
2. Modélisation et modification
Il n'y a pas besoin de plâtre, de moules positifs ou négatifs. Il n'y a pas non plus de processus de séchage, ce qui signifie que le technicien passe moins de temps à attendre. Au lieu de cela, il peut passer directement à la modélisation et à la modification du scan. Le positionnement et le modelage ne prennent pas plus de trois minutes. Le rembourrage ou la mousse peuvent être ajoutés en conséquence.
3. Impression
Vient ensuite le processus d'impression. Une série de rayons infrarouges rapides détermine le contour du membre, sur lequel un modèle d'orthèse peut être construit, à l'aide d'un scanner portable et d'une tablette. Le processus d'impression peut prendre entre 2 et 24 heures. Cela peut être long et c'est peut-être plus long que ce qui est préférable. Cependant, la technologie de l'impression 3D se développe rapidement et nous pouvons nous attendre à ce que l'impression prenne de moins en moins de temps à l'avenir.
4. Nettoyage
Enfin, le nettoyage après l'impression prend une dizaine de minutes. Il est également possible d'ajouter des bandes velcro en utilisant les boucles à travers les passants de la ceinture.
Que signifie tout cela en pratique ?
Limites de la fabrication manuelle d'orthèses
Le processus de fabrication manuelle peut prendre jusqu'à deux jours, séchage compris. Le technicien doit passer la majeure partie de ce temps à travailler sur l'orthèse, ce qui le prive de son travail avec les patients et d'autres aspects de son travail.
La fabrication traditionnelle nécessite également plusieurs matériaux différents, tels que le plâtre, une mousse plastaformée et un thermoplastique, ainsi qu'une variété d'outils de mesure et de façonnage. Malheureusement, quelles que soient l'expertise et l'expérience des techniciens orthopédistes, la fabrication manuelle est sujette à des erreurs. Lorsqu'il s'agit de cas plus complexes, le processus peut devoir être recommencé depuis le début.
En plus de tout cela, la production de plusieurs orthèses personnalisées de même qualité est un défi. Pour le technicien, cela peut signifier un processus long et désordonné qui nécessite beaucoup de planification et de préparation.
Le flux de travail 3D est conçu pour répondre à cette question.
Comment la technologie 3D change la fabrication des orthèses
En pratique, l'impression 3D offre un processus plus simplifié et rationalisé pour les techniciens orthopédistes. Les techniciens peuvent sauter l'étape manuelle intensive du moulage du plâtre et consacrer leur temps à d'autres tâches. Cela signifie également qu'à long terme, il y a moins besoin d'un grand espace de travail pour abriter les machines, les outils et tous les modèles d'orthèses.
Un autre changement important est que la numérisation 3D est une méthode de mesure beaucoup plus précise et exacte. Les inexactitudes commises par l'imprimante 3D sont rares. En outre, le stockage numérique permet au technicien orthopédiste de trouver, modifier et réutiliser toutes les informations relatives à l'orthèse de son patient, tout en n'occupant aucun espace et en réduisant considérablement la quantité de déchets. Si une modification ou plusieurs orthèses personnalisées sont nécessaires, le technicien peut facilement accéder aux données stockées et fabriquer un nouveau modèle en appuyant simplement sur un bouton.
Enfin, une solution d'impression 3D peut réduire considérablement le temps consacré aux tâches manuelles et répétitives. Pour les techniciens orthopédistes, cela signifie plus de temps à consacrer à chaque patient, une communication plus facile et de grandes chances de produire des orthèses parfaitement adaptées.
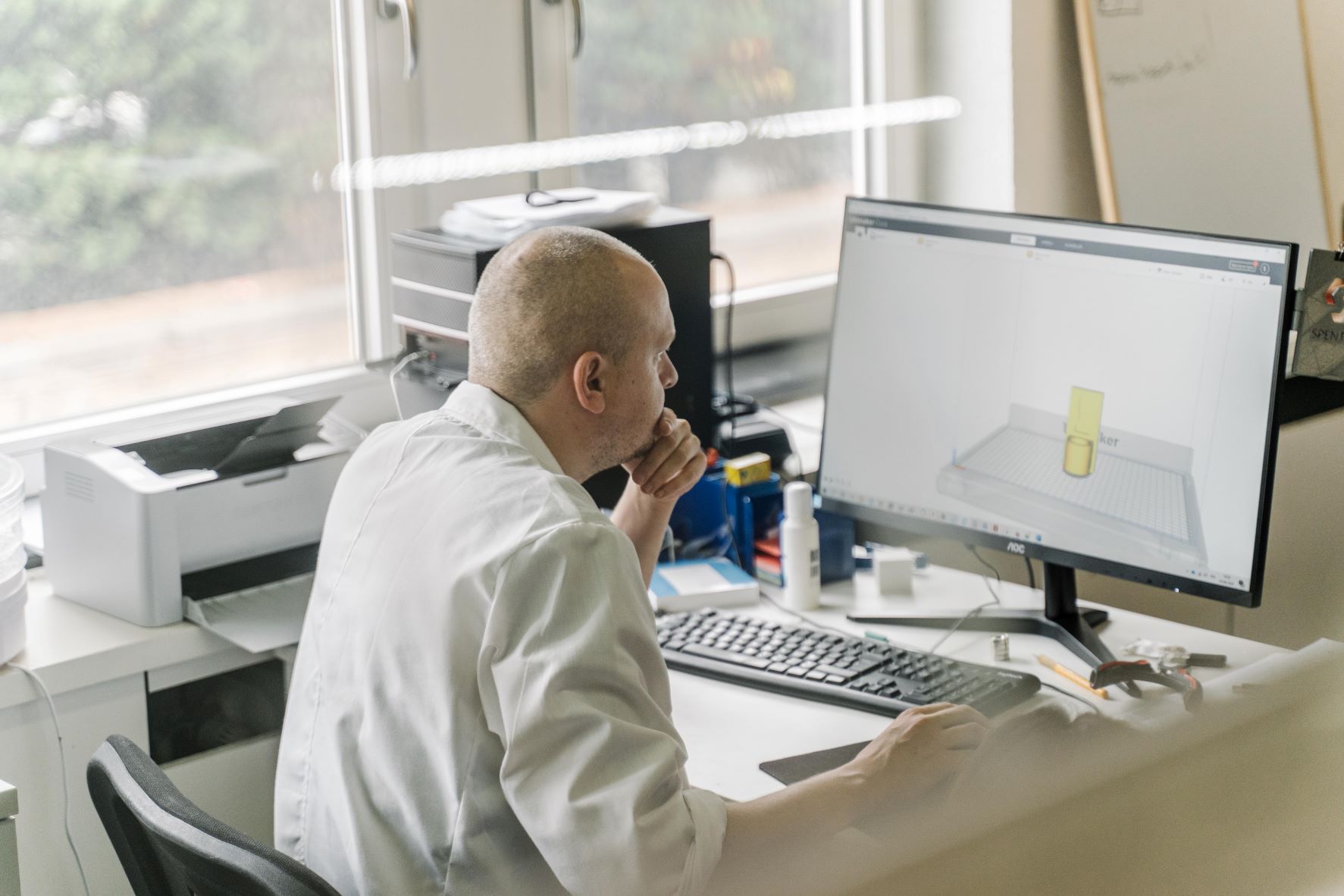
AFOs imprimés en 3D
Cette technologie a déjà prouvé qu'elle apportait une valeur importante au domaine de l'orthopédie, notamment aux AFO. En particulier, des études comme celle de Cha, Yong Ho, et al. montrent le grand potentiel des AFO imprimées en 3D, tant pour les praticiens que pour les patients. Une autre étude, réalisée par Dal Maso, Alberto et Francesca Cosmi, a examiné la procédure de conception d'une AFO imprimée en 3D entièrement personnalisée. L'étude a conclu que le processus peut être facilement automatisé, réduisant ainsi les délais et les coûts de l'ensemble du processus, tout en fournissant une AFO confortable et pratique pour le patient.
La plus grande préoccupation concernant le flux de travail de l'impression 3D est peut-être le temps. Il faut jusqu'à 24 heures pour imprimer l'orthèse, ce qui peut sembler long. Pourtant, une fois lancée, l'imprimante fonctionne de manière autonome, sans avoir besoin d'un opérateur. En moyenne, seules 10 minutes sont nécessaires pour modéliser l'AFO. Sur les 24 heures que dure le processus, cela signifie que seulement 0,5 % de la production nécessite une intervention humaine réelle.
Si la fusion de la technologie 3D avec l'orthopédie peut sembler intimidante pour le technicien orthopédiste, les avantages sont nombreux. L'objectif de cette technologie n'est pas de se substituer au travail et à l'expertise des techniciens, mais plutôt de rendre leur travail plus significatif et plus efficace. Elle leur donne plus de temps pour se concentrer sur les patients et développer des solutions pour eux, plutôt que de passer du temps sur des tâches répétitives ou administratives.
À l'adresse Spentys, nous avons récemment intégré une nouvelle fonctionnalité à notre logiciel, spécialement conçue pour la conception et la fabrication d'AFO. Vous n'avez pas besoin de connaissances techniques préalables pour utiliser notre plateforme et nous vous guiderons tout au long du processus, en veillant à ce qu'il s'adapte à votre flux de travail habituel.
Commencez par réserver votre appel avec un spécialiste dès aujourd'hui.